Our Products
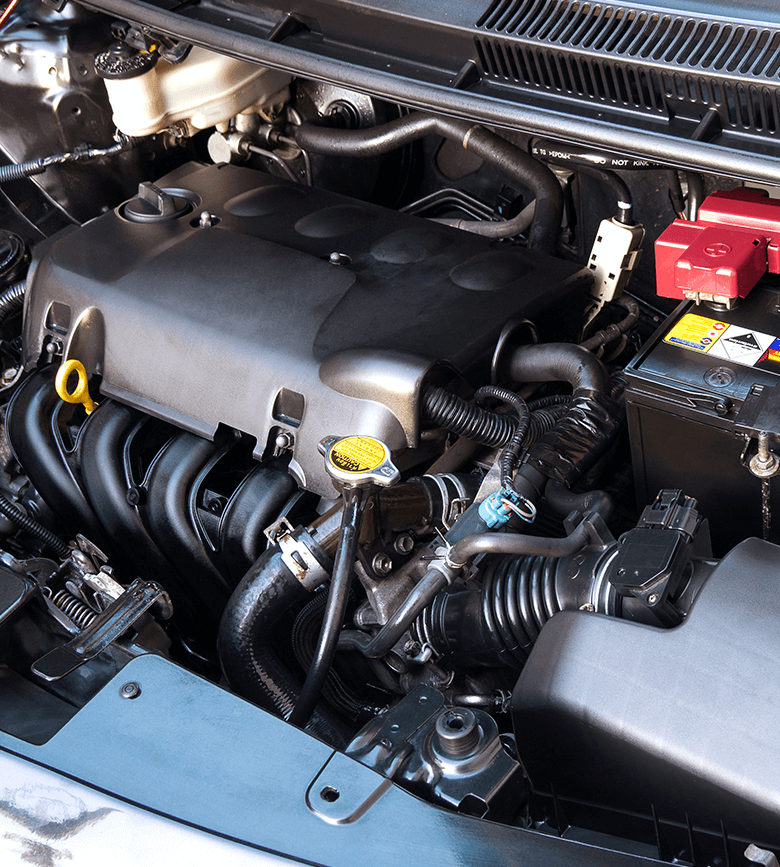
MAXXPOL® Polyamide (PA6)
Engineering Thermoplastics
Polyamide (PA, also popularly known as Nylon) is one of the semi-crystalline engineering thermoplastics. It is a low-density material with high thermal stability and outstanding wear resistance. Good coefficients of friction, impact strength, very good temperature and chemical resistance, especially to oil, making polyamide one of the most important engineering thermoplastics. Polyamides are usually named with numbers (PA6, PA6.6, PA11, PA12, PA6.10, PA6.12, etc.) and thus provide an indication of the molecular structure of the polymer. Depending on the structure of the polyamide, the application limits range from around –30°C (PA 11 and PA 12: –70°C) to over +100°C, with short-term temperatures of around 140°C to 180°C being possible.
PA6 is widely used in a variety of application segments due to its known strength, elasticity and durability. These three features make PA6 one of the most appreciated polyamides used in different industries. In addition, PA6 can withstand sustained contact with a wide variety of chemicals, high temperatures and high pressure. Because of these unique features, PA6 is considered the most widely used polyamide in the world, and it comprises about 60% of the polyamides produced worldwide.
MAXXPOL® PA6 is an unreinforced, medium-viscosity polyamide 6 chip for extrusion applications. This product offers good mechanical properties coupled with thermal properties and has all the primary properties of one unreinforced polyamide 6 used to produce an engineering compound or high-tenacity filament/yarn.
Applications
MAXXPOL® PA6 is significantly used in the following applications:
- Engineering plastics compound
- High tenacity filament/yarn
MAXXPOL® Polymethyl Methacrylate (PMMA)
Engineering Thermoplastics
Polymethyl Methacrylate (PMMA), also known as acrylic, acrylic glass, or plexiglass, is an amorphous thermoplastic having the highest degree of transparency among plastics. Due to the exhibition of glass-like qualities– clarity, brilliance, transparency, translucence – at half the weight, PMMA polymer is often used as a good alternative to glass in products such as shatterproof windows, skylights, and aircraft canopies.
Its excellent characteristics make PMMA the right choice for a wide variety of application segments, such as automobiles, building materials, electric appliances, optical goods as well as products used in everyday life.
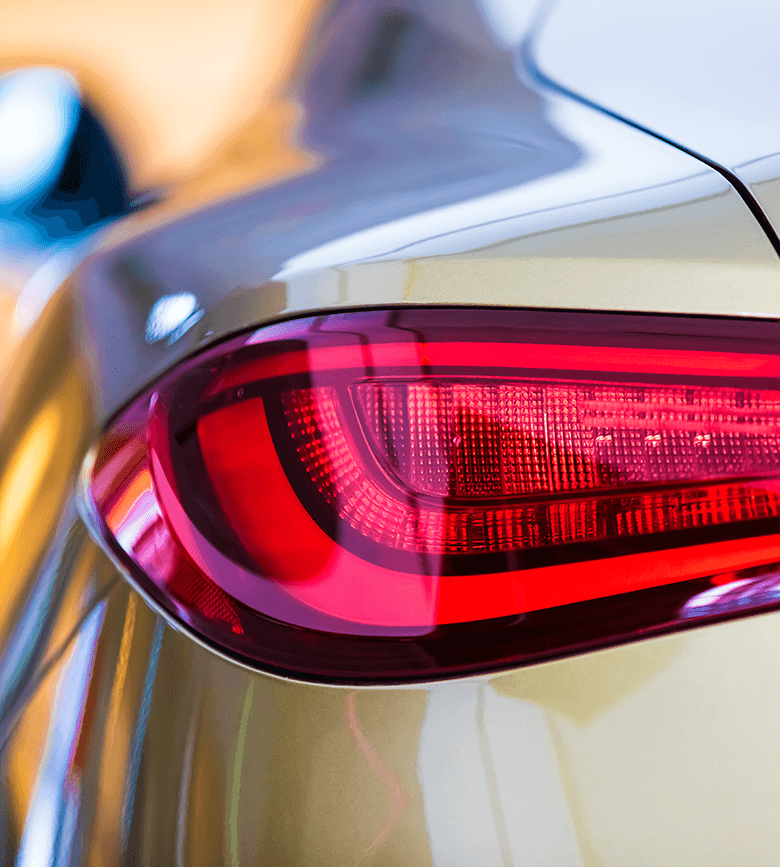
MAXXPOL® PMMA is a heat-resistant, generalpurpose grade PMMA which is suitable for extruded sheets, pipes, and rods, as well as injection molded housewares, automotive taillights, and optical lenses.
Applications
- Automotive: Rear tail lamps, Speedometer covers
- Optical Lens: Sunglasses, Reading glasses
- Lighting Technologies: LED lenses, Streetlight cover, Light guide panels for general LED lighting
- Displays: Light guide plate, Screens, TVs
- Architectural & Household: Sound barriers, Windows and lighting fixtures, Residential and agricultural roofing, Decoration, Luxury sanitary ware
- Medical Devices/Packaging
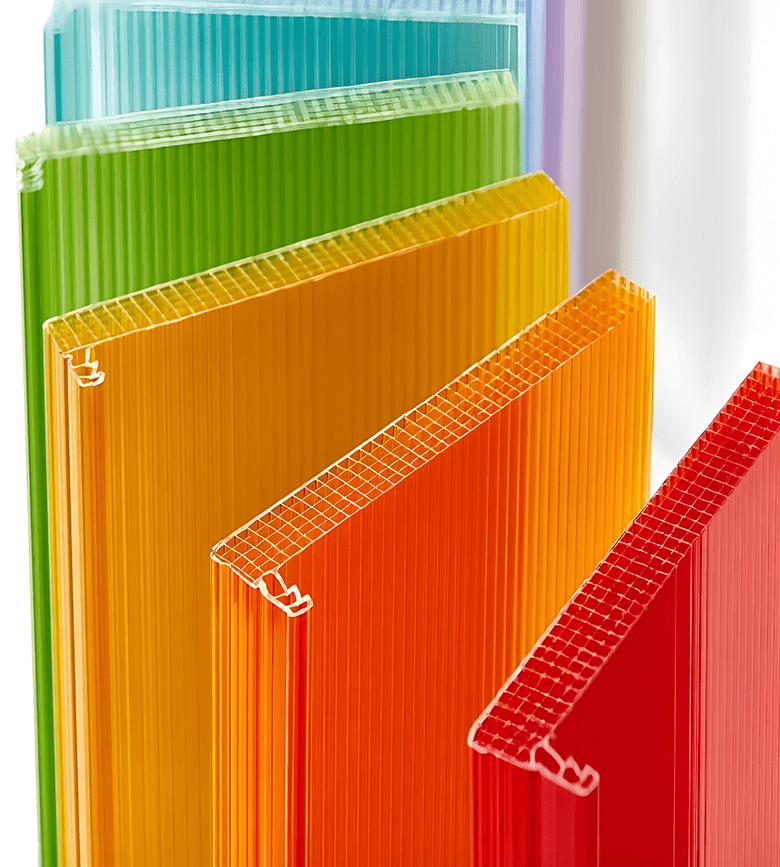
MAXXPOL® Polycarbonate (PC)
Engineering Thermoplastics
Polycarbonate (PC) is one of the amorphous thermoplastics which has a unique property profile compared to other thermoplastics. It is noted above all for its combination of properties of high transparency, high heat resistance and very good impact strength, even at very low temperatures.
Toughness and dimensional stability, as well as a high creep modulus and good electrical insulation properties, are among the advantages.
Key Features
- High Transparency
Light Transmission (Up to 90%) - Exceptional Impact Resistance
Suitable for industrial applications at TRoom & below - Dimensional Stability
Low in shrinkage & CTE - High Heat Resistance
High Tg (145°C)
MAXXPOL® PC resin portfolio offers an optimized set of products designed for various applications in the extrusion, injection molding, optical media markets and compounding markets.
Applications
- Optical storage media: CDs & DVDs
- Electrical & Electronics: Switches & Cases
- Automotive: Headlamps & Lenses
- Building & Construction: Streetlight covers & Lenses for LED lights
- Sheet: Roofing & Glazing
- Consumer: Suitcase, Furniture,
Juicers & blenders
MAXXPOL® Polyolefin Elastomer (POE)
Polymer Modifiers
Polyolefin elastomers (POEs) are a class of materials that bridge the chemistry between rubber and plastic to make new possibilities. They are a range of copolymers based on metallocene catalysis utilizing butene or octene comonomers. POEs can offer exceptional performance with an outstanding balance of toughness & stiffness in compounded products.
MAXXPOL® POE is ethylene octene (EOR) or ethylene butene copolymer (EBR), which is an excellent impact modifier for plastics and designed to offer customers improved melt strength, and processability in a wide variety of applications, including injection molding, extrusion blow molding, blown and casted film, and profile extrusion.
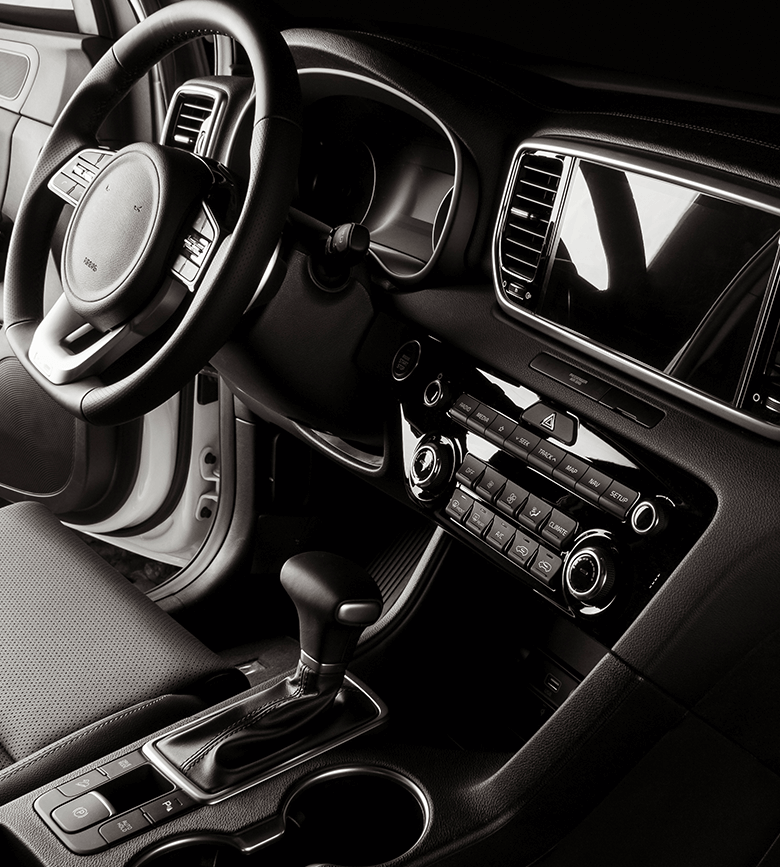
This product exhibits excellent plastic and elastomeric properties, including outstanding toughness. It is in the free-flowing pellet form and has excellent processability. MAXXPOL® POE acts as a premium low-temperature impact modifier and results in outstanding tear strength and toughness.
Applications
- Automotive interior & exterior parts
- Soundproof
- Shoe sole, foam, and footwear
- Wire and cable coatings
- Compounding and thermoplastic olefins (TPO)
- Plastics modification
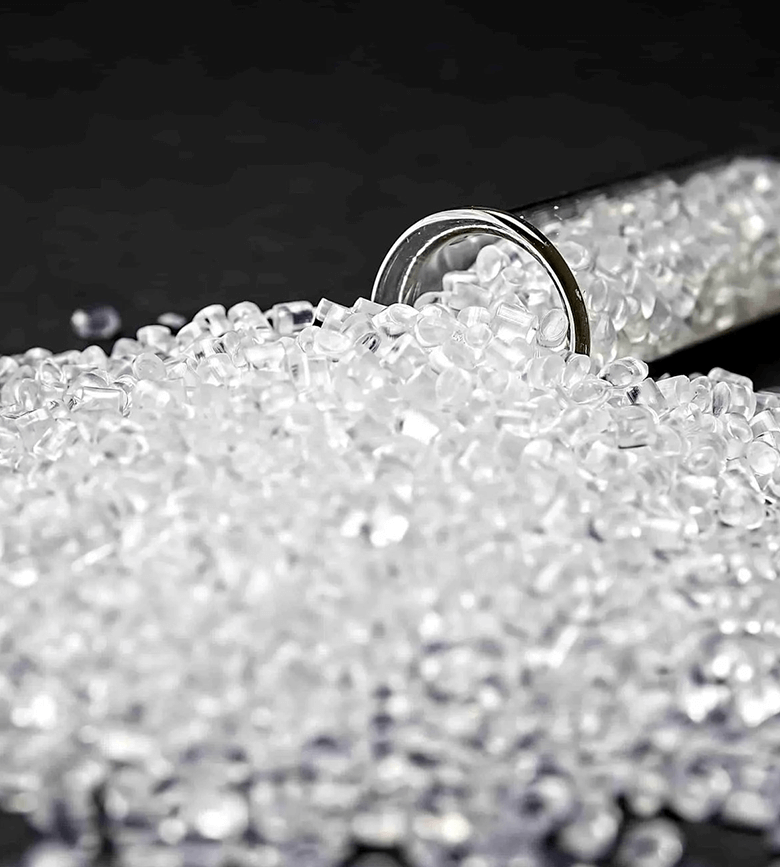
MAXXPOL® Propylene/ Ethylene Elastomers
Polymer Modifiers
When it comes to creating new possibilities for product innovation, MAXXPOL® Propylene/ Ethylene Elastomers with inimitable polymer features (such as toughness, cling, sealability, softness, clarity, dispersion, adhesion, elasticity and flexibility) can be used.
They are semi-crystalline copolymers composed of isotactic propylene repeat units with random ethylene distribution and are compatible with other polyolefinic materials.
MAXXPOL® Propylene/Ethylene Elastomers have exceptional performance for thermoplastic and polyolefinic blends, where a balance of flexibility, transparency and impact performance is a necessity. They can also improve filler dispersion and acceptance.
Applications
MAXXPOL® Propylene/Ethylene Elastomers are suitable for a variety of film and compounding functions which require high filler acceptance, such as sound deadening sheets and masterbatches. They are typically used for calendered or extruded sheets/ profiles, foamed or blown molded goods, thermoformed products and injection molded goods.
These products offer outstanding adhesion to conventional or metallocene PP and PE.
They also possess excellent elasticity, toughness, melt strength, low seal initiation temperature, and remarkable chemical resistance giving long-term ageing.
It can be used in hot melt adhesives (HMAs) and as a viscosity modifier or process aid in extrusion and injection molding applications.
- Compounding
- PP/TPE Modification
- Injection Molding
- Blown and Cast Film
- Blown Molded Goods
- Calendered Profiles/Sheeting
- Extruded Profiles/Sheeting
- Hot Melt Adhesives
MAXXPOL® Maleated Polyethylene (PE-g-MAH)
Polymer Modifiers
MAXXPOL® maleic anhydride grafted ethylene copolymers are used to achieve the delicate balance between stiffness and impact strength of a variety of engineered thermoplastics and other technical polymers. They are based on maleic anhydride functionalized elastomeric and polyolefinic polymers and are produced through reactive extrusion.
MAXXPOL® Maleated Polyethylenez enhances the impact strength of engineering thermoplastics and technical polymers at a broad range of service temperatures. They can also improve homogeneity and surface aspects in filled compounds.
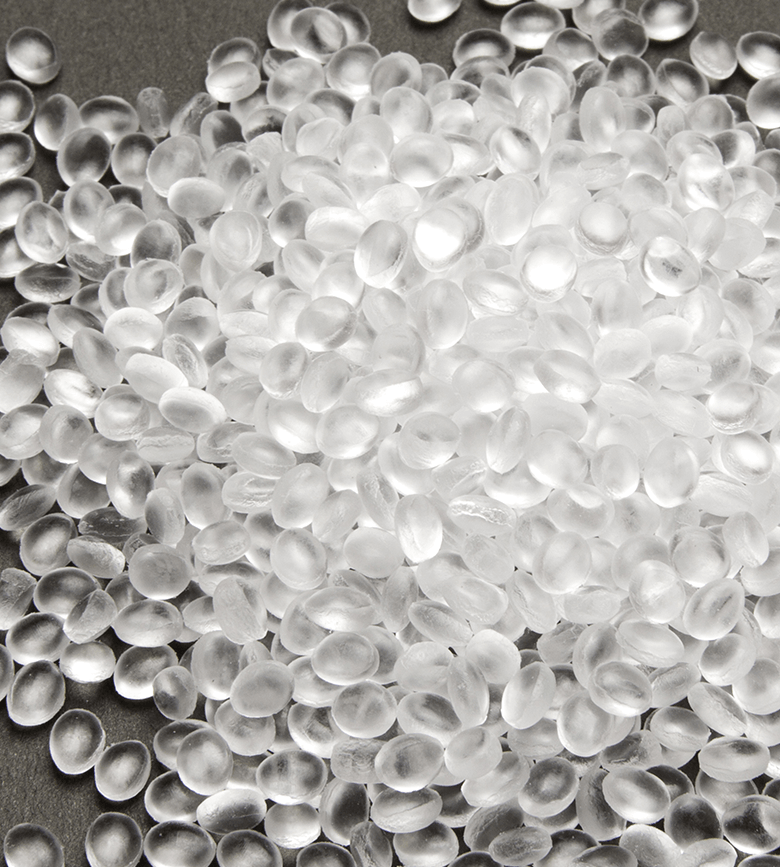
Applications
MAXXPOL® Maleated Polyethylene can be used as an impact modifier for a full range of polyamides (PA6, PA66, PA12, etc.) as well as other engineering thermoplastics and technical polymers (with or without glass fibers, fillers, etc.) at temperatures as low as -20°C. Furthermore, they can provide compatibility between polyolefins and more polar polymers that are capable of interacting with maleic anhydride.
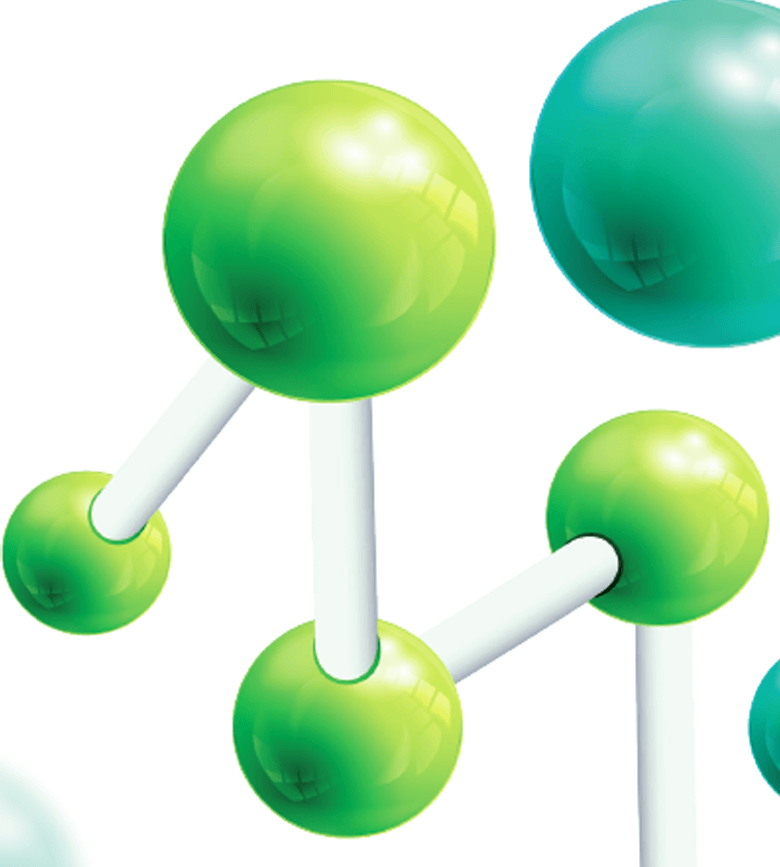
MAXXPOL® Ethylene Propylene Diene Monomer (EPDM) Pellet
EPDM rubber in free-flowing pellet form can be used as a modifier to blend with polyolefins (PP & PE) in injection molding, (such as bumpers), films, sheets, and various types of automobile parts. It exhibits excellent processability, weather resistance, heat ageing resistance, and cold and chemical resistance.
MAXXPOL® EPDM Pellets with narrow molecular weight distribution and high ethylene content offer a fast cure rate, high filler ability and excellent mutual miscibility with polypropylene.
Applications
- Automotive sealing strip
- Automotive rubber hoses & cooling tubes
- Damper profiles
- Waterproof roll covers
- Plastic cement track applications
- Treadmills
- Shoe materials